Flexible product packaging has become an increasingly popular method across many industries. Flexible packaging is perhaps most common in the food industry, as it allows the manufacturer to provide the highest possible volume of products per package. Flexible packaging can be created from a variety of materials, the most common being plastic, paper, and foil, and can take on a number of different forms, from bags to pouches to sleeves to wraps. Though the shape and size of flexible packaging may change from product to product, the practices used to develop such packaging often remain the same. Indeed, most manufacturing companies adhere to the same practices when developing flexible product packaging. This guide explores some of the best practices in flexible package development and the importance of adhering to such practices, regardless of industry.
Assess Existing Packaging
When considering best practices in flexible package development, it’s always best to assess your company’s current processes for manufacturing flexible packaging. This is the most effective way to analyze which processes work well and which could do with some adjustment. In analyzing your current processes, you may also discover instances where you can consolidate your procedures. For products that are packaged in nearly identical packages with few minor differences, you may be able to slightly alter production so they utilize the same materials and packaging procedures. This will help streamline processes in your company and can even help decrease your company’s carbon footprint in the long run. This analysis allows you to cut out the waste to create a more efficient, sustainable practice for producing flexible packaging.
Outline All Packaging Requirements
Flexible packaging requirements can vary greatly, depending on the intended use of the packaging and the industry in which it will be used. You should outline all packaging requirements before you begin manufacturing the package itself. These requirements may include product compatibility needs, methods for opening and sealing the product, and the intended printing method for the package label. You will also need to consider the type of product that will be stored inside the packaging. Certain products will require that no moisture, light, or drastic temperature changes permeate the packaging. Outlining these packaging requirements as early as possible will ensure that the product maintains its integrity throughout the course of its journey from manufacturing facility to retail shelf.
Match the Machine to the Material
Certain printing methods are more effective when used in tandem with specific materials. Additionally, certain machines are only intended for use with specific packaging materials (i.e. inkjet printers require material with an inkjet-receptive coating). Therefore, it’s important that you match the machine and packaging material to ensure the most efficient production possible. Optimizing specific materials and machinery to suit specific needs will allow you to streamline procedures throughout the entire process. When selecting a high-quality packaging label printing machine, be sure that it will accommodate your specific packaging materials, whether they are paper or synthetic material such as Sihl’s ARTYSIO Polypropylene films that are used in the Afinia FP-230 Flexible Packaging Press.
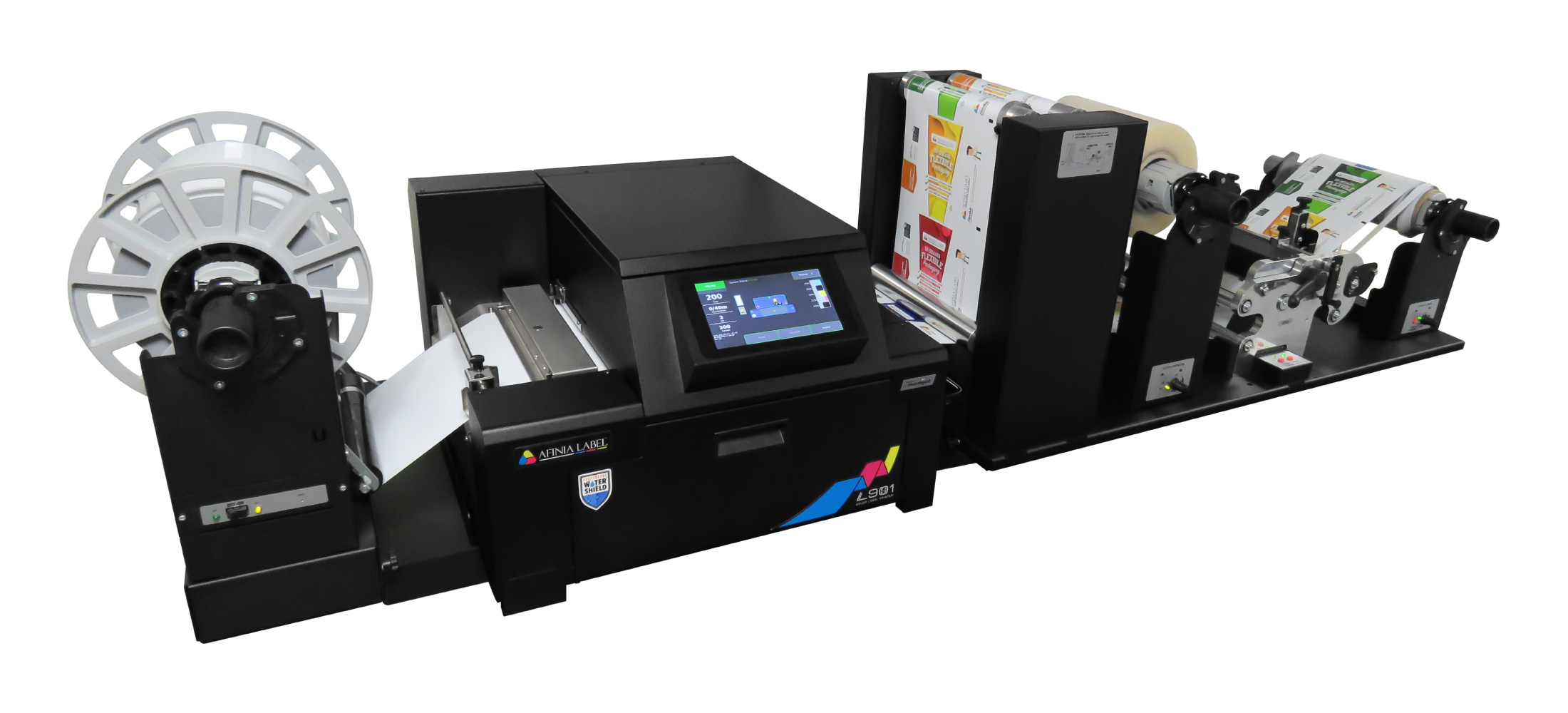
These recyclable films by Sihl — used in conjunction with the Afinia FP-230 — provide strong barriers and sealing properties, making them perfect for a wide range of flexible packaging applications. The Afinia FP-230 utilizes the Afinia L901 Plus Label Printer to produce vibrant, full-color printed flexible packaging material on rolls up to 9″ wide with a maximum speed of approximately 60 feet per minute. The water-based inks have been approved for food packaging when combined with the in-line cold lamination. Finally, the finished roll of printed and laminated packaging material is trimmed to a specific width using the two rotary knives. Contact us today for more information about the Afinia FP-230.